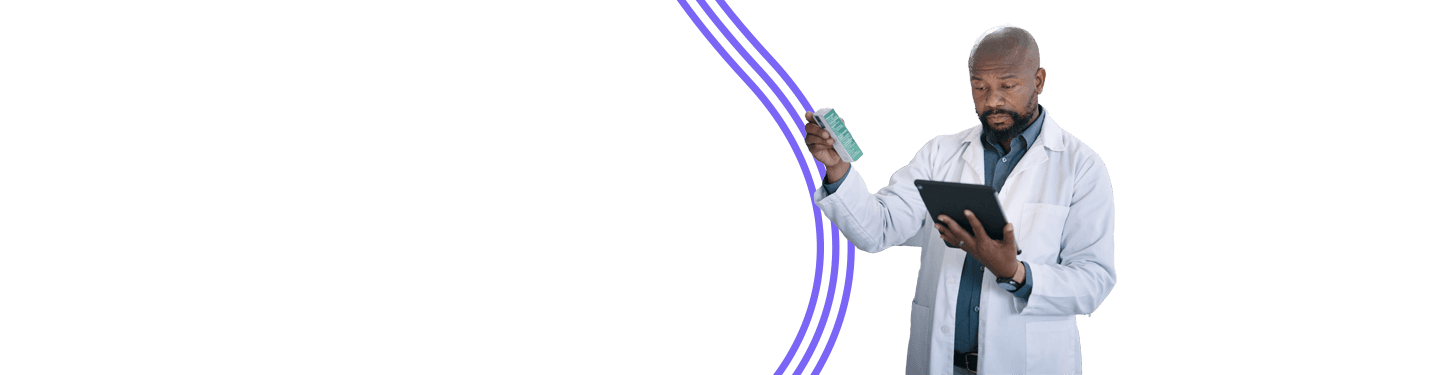
Case Study: Major Global Pharmaceutical Company
How a pharmaceutical giant accelerates regulatory submissions and eliminates errors
About our customer
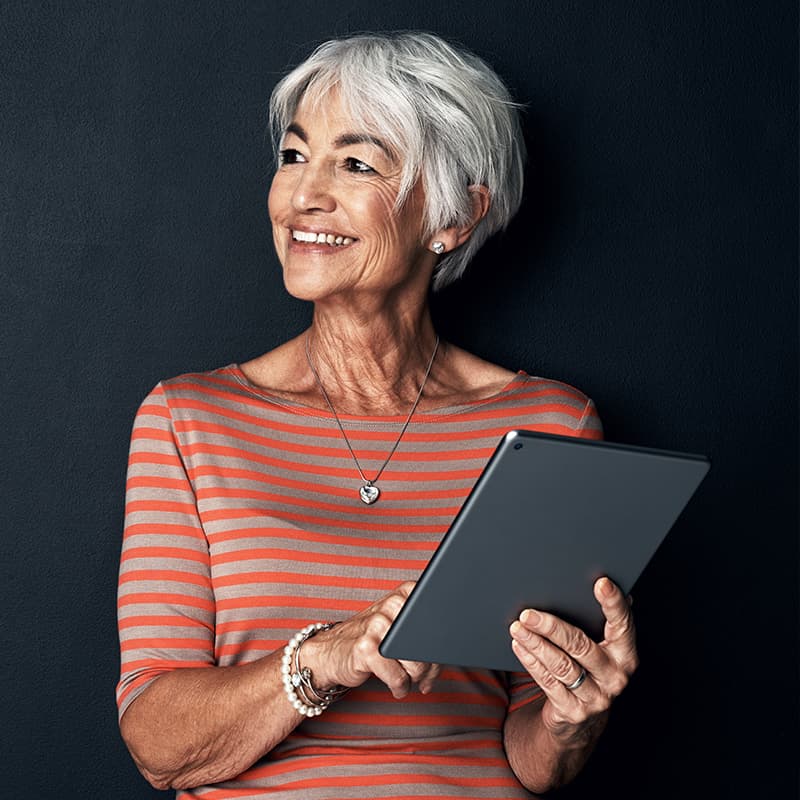
This leading global pharmaceutical company has been innovating and producing therapies for oncology, neuroscience, cardiovascular, metabolism and infectious diseases for nearly 70 years, delivering life-enhancing drugs and healthcare relief worldwide.
Since Ricoh assumed responsibility for the pharmaceutical company's production centers, the FDA and other regulatory bodies have not returned any submission packages for rework due to errors.
Challenge
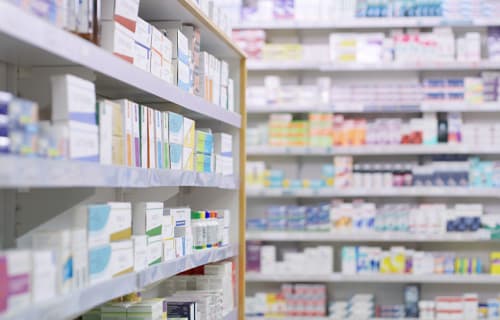
Complex regulatory approval process
Varied regional document requirements
Prolonged document submission times
Returned packages for missing documents or errors
Pharmaceutical companies face complex regulatory approval processes. While the U.S. Food and Drug Administration is the main regulatory body, all regions have their own regulatory entities with required protocols and preferences for reviewing documentation. These require briefing booklets, follow-up documents, and approved promotional materials.
Despite having global in-house production offices, many companies have downsized due to cost pressures and recruitment challenges, causing delays and submission errors.
Solution
Ricoh's highly automated process for producing regulatory materials has accelerated submission times by at least three days.
Managed Print Services for package production and assembly
Installed hardware and software to improve workflow
Optimized workspace to increase efficiency and expedite processing times
Adopted quality control measures
Ricoh took over document production, setting up local submission offices with trained staff in emerging markets. We analyzed print volumes for staffing, equipped offices with advanced hardware/software and stored documents in a secure CMS for inspection and approval.
The new workflow improved file processing and printing efficiency. Ricoh also streamlined equipment, ensured document accuracy with rigorous quality control, introduced a Service Excellence Operations Guide and collaborated on automation solutions like web submission software.
Results
No defects or returned packaging
100% on-time delivery of submissions
Reduced operational costs
Increased number of submissions per month
Since Ricoh began producing regulatory documents, there have been no defects or returns, achieving 100% on-time delivery and expediting drug approvals. Ricoh's on-site staffing model reduced costs, improved productivity and increased monthly regulatory submissions globally — typically 100 or more per month.
Automation sped up submission times by 3-5 days. Impressed with Ricoh's technology and expertise, the pharmaceutical company assigned additional scanning tasks to the production office.
Discover how Ricoh can help your organization drive productivity, streamline workflows and reduce costs through Managed Print Services or contact us to learn more.